Articles
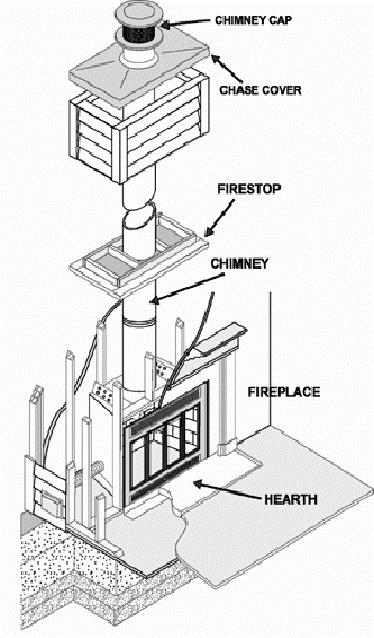
by Nick Gromicko and Ethan Ward | Source: http://www.nachi.org/factory-built-fireplaces.htm#ixzz2ln9iM4qJ There’s nothing like coming home and warming up next to a roaring fire during the long, cold months of winter, or even chilly evenings in any season. Long commutes to work in the cold and the increasingly short hours of daylight in the fall and winter are made more bearable by the comfort and familiarity of family gatherings by the fire. It may be for this reason that some type of wood-burning enclosure has remained a staple of many households, even though open fire is no longer a necessity for cooking and heating. With this in mind, let's take a look at one of the more modern options available, the factory-built fireplace. What is a factory-built fireplace and how does it differ from a masonry fireplace?
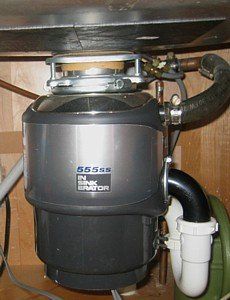
by Nick Gromicko and Kenton Shepard | Source: http://www.nachi.org/garbage-disposals.htm#ixzz2lnINbwBh Garbage disposals are residential and commercial appliances designed to shred food waste so that it can fit through plumbing. They are usually electrically powered (although occasionally powered by water pressure) and are installed beneath sinks. Despite the convenience afforded by garbage disposals, the strain they can place on septic systems should be weighed against any potential benefits they might provide. Why Use a Garbage Disposal ? When food waste is discarded into the trash, it places an enormous burden on waste management systems and harm the environment. Garbage disposals reduce the severity of these problems by routing food waste into septic systems or sewers instead of landfills. The following are a few specific problems associated with food waste that can be curbed through the use of a garbage disposal: It must be collected and transported long distances to landfills and waste treatment facilities. In landfills, food scraps decompose and produce methane gas, which contributes to global warming. Note: The above points must be weighed against the added expense of treating food waste in sewer systems and transporting it from septic systems. Garbage Disposals and Septic Systems If a garbage disposal discharges into a septic tank, it can place significant strain on the septic system. The amount of waste that enters the tank, particularly grease and suspended solids, will increase considerably. This load increase requires that the septic tank be pumped more often than would otherwise be required. The New York Septic Code counts the presence of a garbage disposal the same as an extra room in a house when they estimate the load placed on a septic tank. The additional strain will also reduce the life span of the septic system. Septic systems can be designed to accommodate food waste but, in general, they are not. Wiring Inspection The National Electrical Code (NEC) does not require a garbage disposal to have GFCI protection. GFCI protection for this appliance is optional. The vibration caused by the operation of a garbage disposal can cause electrical connections to separate. Check for any loose connections in the wire compartment box at the base of the disposal. Garbage disposals should be either hardwired or connected to an outlet through a grounded electrical outlet. A dedicated circuit is generally recommended, although a circuit that is shared with a dishwasher is sometimes appropriate. The best authority on this distinction is the disposal’s user manual. Maintenance and Operation Suggestions That Inspectors Can Pass on to Their Clients: Put only small quantities of food into the disposal at a time. Large food scraps should be cut into smaller pieces before entering the disposal. Never put anything down the disposal that is not food or water. Bottle caps, aluminum foil, and other non-food items can damage the disposal or get stuck in piping. Run water while using the disposal, and for approximately 30 seconds after you turn it off. Food scraps will flow through the piping more easily if they are pushed along by water. Cold water is better than warm water for this purpose because it will force fats and grease to congeal and harden, allowing them to move more easily through pipes. Warm water can be run through the disposal while it is not in operation. Ice can be used to clear off solidified grease and other debris from the blades in a garbage disposal. The garbage disposal should only be used to grind non-fibrous, leftover food. If in doubt as to whether something can be put in the disposal, err on the side of caution and put it in the trash instead. The following items should never be put in a disposal: items that are hard enough to dull the blades, such as shells from shellfish or bones; food that is highly fibrous, such as corn husks, artichokes, pineapples, potato peels, asparagus, or celery should enter a disposal only in small quantities or avoided entirely. These foods take a long time to grind and can clog the disposal or the plumbing. grease or household oils; or chemicals. In summary, garbage disposals have the potential to limit the amount of household trash that must be taken away to waste management facilities. They can also place additional strain on septic systems and, for this reason, they should be used infrequently. Inspectors can test disposals for leaks and proper wiring, but they should beware not to do anything that might cause them to break. Inspectors should be prepared to communicate all of this knowledge to their clients.
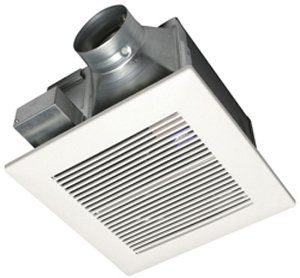
by Nick Gromicko and Kenton Shepard | Source: http://www.nachi.org/bathroom-ventilation-ducts-fans.htm#ixzz2lnG5Zbo4 Bathroom ventilation systems are designed to exhaust odors and moist air to the home's exterior. Typical systems consist of a ceiling fan unit connected to a duct that terminates at the roof. Fan Function The fan may be controlled in one of several ways: Most are controlled by a conventional wall switch. A timer switch may be mounted on the wall. A wall-mounted humidistat can be pre-set to turn the fan on and off based on different levels of relative humidity. Newer fans may be very quiet but work just fine. Older fans may be very noisy or very quiet. If an older fan is quiet, it may not be working well. Inspectors can test for adequate fan airflow with a chemical smoke pencil or a powder puff bottle, but such tests exceed InterNACHI's Standards of Practice. Bathroom ventilation fans should be inspected for dust buildup that can impede air flow. Particles of moisture-laden animal dander and lint are attracted to the fan because of its static charge. Inspectors should comment on dirty fan covers. Ventilation systems should be installed in all bathrooms. This includes bathrooms with windows, since windows will not be opened during the winter in cold climates. Defects The following conditions indicate insufficient bathroom ventilation: moisture stains on walls or ceilings; corrosion of metal; visible mold on walls or ceilings; peeling paint or wallpaper; frost on windows; and high levels of humidity. The most common defect related to bathroom ventilation systems is improper termination of the duct. Vents must terminate at the home exterior. The most common improper terminations locations are: mid-level in the attic. These are easy to spot; beneath the insulation. You need to remember to look. The duct may terminate beneath the insulation or there may be no duct installed; and under attic vents. The duct must terminate at the home exterior, not just under it. Improperly terminated ventilation systems may appear to work fine from inside the bathroom, so the inspector may have to look in the attic or on the roof. Sometimes, poorly installed ducts will loosen or become disconnected at joints or connections. Ducts that leak or terminate in attics can cause problems from condensation. Warm, moist air will condense on cold attic framing, insulation and other materials. This condition has the potential to cause health and/or decay problems from mold, or damage to building materials, such as drywall. Moisture also reduces the effectiveness of thermal insulation. Mold Perhaps the most serious consequence of an improper ventilation setup is the potential accumulation of mold in attics or crawlspaces. Mold may appear as a fuzzy, thread-like, cobwebby fungus, although it can never be identified with certainty without being lab-tested. Health problems caused by mold are related to high concentrations of spores in indoor air. Spores are like microscopic seeds, released by mold fungi when they reproduce. Every home has mold. Moisture levels of about 20% in materials will cause mold colonies to grow. Inhaling mold spores can cause health problems in those with asthma or allergies, and can cause serious or fatal fungal infections in those with lung disease or compromised immune systems. Mold is impossible to identify visually and must be tested by a lab in order to be confidently labeled. Inspectors should refrain from calling anything “mold” but should refer to anything that appears as mold as a material that “appears to be microbial growth.” Inspectors should include in their report, and in the inspection agreement signed by the client, a disclaimer clearly stating that the General Home Inspection is an inspection for safety and system defects, not a mold inspection. Decay, which is rot, is also caused by fungi. Incipient or early decay cannot be seen. By the time decay becomes visible, affected wood may have lost up to 50% of its strength. In order to grow, mold fungi require the following conditions to be present: oxygen; temperatures between approximately 45° F and 85° F; food. This includes a wider variety of materials found in homes; and moisture. If insufficient levels of any of these requirements exist, all mold growth will stop and fungi will go dormant. Most are difficult to actually kill. Even though mold growth may take place in the attic, mold spores can be sucked into the living areas of a residence by low air pressure. Low air pressure is usually created by the expulsion of household air from exhaust fans in bathrooms, dryers, kitchens and heating equipment.
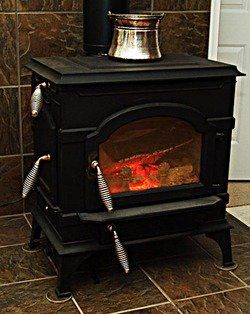
by Nick Gromicko | Source: http://www.nachi.org/wood-burning-stoves.htm#ixzz2lnALrmPr A wood-burning stove (also known as a wood stove) is a heating appliance made from iron or steel that is capable of burning wood fuel. Unlike standard fireplaces, wood stoves are typically contained entirely within the living space, rather than inset in the wall. Wood stoves come in many different sizes, each suited for a different purpose: Small stoves are suitable in single rooms, seasonal cottages or small, energy efficient homes. These models can also be used for zone heating in large homes where supplemental heating is needed. Medium-size stoves are appropriate for heating small houses or mid-size homes that are intended to be energy-efficient and as inexpensive as possible to maintain. Large stoves are used in larger homes or older homes that leak air and are located in colder climate zones. To ensure safe and efficient use of wood-burning stoves, inspectors can pass along the following tips to their clients: Never: burn coal. Coal burns significantly hotter than wood, posing a fire hazard; burn materials that will emit toxic chemicals, such as wood that has been pressure-treated or painted, colored paper, gift wrap, plastic, plywood, particleboard, or questionable wood from furniture; burn wet wood. Generally speaking, it takes six months for cut, stored wood to dry out and be ready for use in wood-burning stoves; burn combustible liquids, such as kerosene, gasoline, alcohol or lighter fluid; let small children play near a lit wood-burning stove. Unlike standard fireplaces, the sides of which are mostly inaccessible, all sides of wood stoves are exposed and capable of burning flesh or clothing; or let the fire burn while the fire screen or door is open. Always: use a grate to hold the logs so that they remain secured in the stove and the air can circulate adequately to keep the fire burning hot; keep the damper open while the stove is lit; dispose of ashes outdoors in a water-filled, metal container; check smoke alarms to make sure they are working properly; and periodically remove the stovepipe between the stove and the chimney so that it can be inspected for creosote. Homeowners may want to hire a professional to perform this service. Efficiency and Air Pollutants While federal and state governments crack down on vehicle and industrial emissions, they do relatively little to limit the harmful air pollution emitted from wood stoves. The problem is so bad that, in many areas, such as Chico, Caifornia (pictured at right), the smoke from wood stoves is the largest single contributor to that city's air pollution. Smoke from wood stoves can cause a variety of health ailments, from asthma to cancer. To mitigate these concerns, the EPA sets requirements for wood-stove emissions based on the design of the stove: 4.1 grams of smoke per hour (g/h) for catalytic stoves, and 7.5 g/h for non-catalytic stoves. Some state laws further restrict airborne particulates, and many new models emit as little as 1 g/h. These two approaches -- catalytic and non-catalytic combustion -- are described briefly as follows: In catalytic stoves, the smoky exhaust passes through a coated, ceramic honeycomb that ignites particulates and smoke gasses. Catalysts degrade over time and must eventually be replaced, but they can last up to six seasons if the stove is used properly. Inadequate maintenance and the use of inappropriate fuel result in an early expiration of the catalyst. These stoves are typically more expensive than non-catalytic models, and they require more maintenance, although these challenges pay off through heightened efficiency. Non-catalytic stoves lack a catalyst but have three characteristics that assist complete, clean combustion: pre-heated combustion air introduced from above the fuel; firebox insulation; and a large baffle to create hotter, longer air flow in the firebox. The baffle will eventually need to be replaced as it deteriorates from combustion heat. The following indicators hint that the fire in a wood-burning stove suffers from oxygen deprivation and incomplete combustion, which will increase the emission of particulates into the air: It emits dark, smelly smoke. An efficient stove will produce little smoke. There is a smoky odor in the house. There is soot on the furniture. The stove is burning at less than 300º F. A flue pipe-mounted thermometer should read between 300º F and 400º F. The flames are dull and steady, rather than bright and lively. To ensure efficiency, practice the following techniques: Purchase a wood-burning stove listed by Underwriters Laboratories. Stoves tested by UL and other laboratories burn cleanly and efficiently. Burn only dry wood. Wood that has a moisture content (MC) of less than 20% burns hotter and cleaner than freshly cut wood, which may contain half of its weight in water. Burn hardwoods, such as oak, hickory and ash once the fire has started. Softwoods, such as pine, ignite quicker and are excellent fire starters. Make sure the stove is properly sized for the space. Stoves that are too large for their area burn inefficiently. Burn smaller wood rather than larger pieces. Smaller pieces of wood have a large surface area, which allows them to burn hotter and cleaner. In summary, wood-burning stoves, if properly designed and used appropriately for the space, are efficient, clean ways to heat a home.
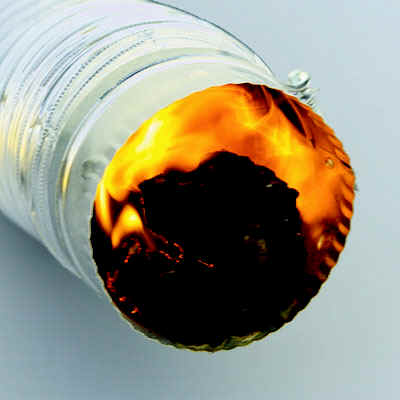
by Nick Gromicko and Kenton Shepard | Source: http://www.nachi.org/dryer-vent-safety.htm#ixzz2ln7mXmXF Clothes dryers evaporate the water from wet clothing by blowing hot air past them while they tumble inside a spinning drum. Heat is provided by an electrical heating element or gas burner. Some heavy garment loads can contain more than a gallon of water which, during the drying process, will become airborne water vapor and leave the dryer and home through an exhaust duct (more commonly known as a dryer vent). A vent that exhausts moist air to the home's exterior has a number of requirements: It should be connected. The connection is usually behind the dryer but may be beneath it. Look carefully to make sure it’s actually connected. It should not be restricted. Dryer vents are often made from flexible plastic or metal duct, which may be easily kinked or crushed where they exit the dryer and enter the wall or floor. This is often a problem since dryers tend to be tucked away into small areas with little room to work. Vent hardware is available which is designed to turn 90° in a limited space without restricting the flow of exhaust air. Restrictions should be noted in the inspector's report. Airflow restrictions are a potential fire hazard. One of the reasons that restrictions are a potential fire hazard is that, along with water vapor evaporated out of wet clothes, the exhaust stream carries lint – highly flammable particles of clothing made of cotton and polyester. Lint can accumulate in an exhaust duct, reducing the dryer’s ability to expel heated water vapor, which then accumulates as heat energy within the machine. As the dryer overheats, mechanical failures can trigger sparks, which can cause lint trapped in the dryer vent to burst into flames. This condition can cause the whole house to burst into flames. Fires generally originate within the dryer but spread by escaping through the ventilation duct, incinerating trapped lint, and following its path into the building wall. InterNACHI believes that house fires caused by dryers are far more common than are generally believed, a fact that can be appreciated upon reviewing statistics from the National Fire Protection Agency. Fires caused by dryers in 2005 were responsible for approximately 13,775 house fires, 418 injuries, 15 deaths, and $196 million in property damage. Most of these incidents occur in residences and are the result of improper lint cleanup and maintenance. Fortunately, these fires are very easy to prevent. The recommendations outlined below reflect International Residential Code (IRC) SECTION M1502 CLOTHES DRYER EXHAUST guidelines: M1502.5 Duct construction. Exhaust ducts shall be constructed of minimum 0.016-inch-thick (0.4 mm) rigid metal ducts, having smooth interior surfaces, with joints running in the direction of air flow. Exhaust ducts shall not be connected with sheet-metal screws or fastening means which extend into the duct. This means that the flexible, ribbed vents used in the past should no longer be used. They should be noted as a potential fire hazard if observed during an inspection. M1502.6 Duct length. The maximum length of a clothes dryer exhaust duct shall not exceed 25 feet (7,620 mm) from the dryer location to the wall or roof termination. The maximum length of the duct shall be reduced 2.5 feet (762 mm) for each 45-degree (0.8 rad) bend, and 5 feet (1,524 mm) for each 90-degree (1.6 rad) bend. The maximum length of the exhaust duct does not include the transition duct. This means that vents should also be as straight as possible and cannot be longer than 25 feet. Any 90-degree turns in the vent reduce this 25-foot number by 5 feet, since these turns restrict airflow. A couple of exceptions exist: The IRC will defer to the manufacturer’s instruction, so if the manufacturer’s recommendation permits a longer exhaust vent, that’s acceptable. An inspector probably won’t have the manufacturer’s recommendations, and even if they do, confirming compliance with them exceeds the scope of a General Home Inspection. The IRC will allow large radius bends to be installed to reduce restrictions at turns, but confirming compliance requires performing engineering calculation in accordance with the ASHRAE Fundamentals Handbook, which definitely lies beyond the scope of a General Home Inspection. M1502.2 Duct termination. Exhaust ducts shall terminate on the outside of the building or shall be in accordance with the dryer manufacturer’s installation instructions. Exhaust ducts shall terminate not less than 3 feet (914 mm) in any direction from openings into buildings. Exhaust duct terminations shall be equipped with a backdraft damper. Screens shall not be installed at the duct termination . Inspectors will see many dryer vents terminate in crawlspaces or attics where they deposit moisture, which can encourage the growth of mold, wood decay, or other material problems. Sometimes they will terminate just beneath attic ventilators. This is a defective installation. They must terminate at the exterior and away from a door or window. Also, screens may be present at the duct termination and can accumulate lint and should be noted as improper. M1502.3 Duct size. The diameter of the exhaust duct shall be as required by the clothes dryer’s listing and the manufacturer’s installation instructions. Look for the exhaust duct size on the data plate. M1502.4 Transition ducts. Transition ducts shall not be concealed within construction. Flexible transition ducts used to connect the dryer to the exhaust duct system shall be limited to single lengths not to exceed 8 feet (2438 mm), and shall be listed and labeled in accordance with UL 2158A. In general, an inspector will not know specific manufacturer’s recommendations or local applicable codes and will not be able to confirm the dryer vent's compliance to them, but will be able to point out issues that may need to be corrected.